Overview
Futamura produces renewable and compostable cellulose films for the food packaging market. Its NatureFlex™ brand is a range of compostable packaging films made from responsibly sourced wood pulp.
Domino Printing Sciences (Domino) and Futamura have collaborated to assess the suitability of laser coding for NatureFlex compostable film products, to give food packaging customers a print-free solution for coding and marking their packaging.
Following initial suitability testing, Domino’s D-Series CO2 Laser was used to code the NatureFlex compostable film and achieved a clean, crisp, white code without affecting the integrity of the original film, changing the chemical composition, or affecting the moisture barrier properties.
Fast Facts
- Established in Japan in 1947, Futamura is a global brand with over 1,500 employees worldwide. Its cellulose film production sites are in Japan, the UK, and the USA.
- Manufacturers use Futamura’s NatureFlex films in the food and beverage industries, including confectionery, snacks, fresh produce, tea, and coffee.
- NatureFlex films are derived from wood pulp sourced from responsibly managed plantations.
- NatureFlex films meet all the global standards for industrial composting, including BS EN13432, and are also certified to the OK Compost Home standard for home compostability.
Project background
Providing businesses with the best possible solutions for coding and marking their products requires an in-depth knowledge of new and emerging packaging trends. At the Domino Laser Academy in Hamburg, Domino’s experts are involved in continual research and experimentation into new substrates.
“We spend a lot of time analysing new packaging materials – both through customer requests and our own investigative work,” says Dr. Stefan Stadler, Team Lead at the Domino Laser Academy.
“Currently, due to the new European regulations around recycled plastics, approximately 95% of the food packaging samples that we are sent to test are post-consumer recycled (PCR) or recyclable plastics. We now have many solutions available for this kind of substrate in our F-Series fibre Laser, and U-Series UV laser ranges.
“However, we predict that in the coming years, requests for compostable solutions will become more prominent – and so we want to ensure that we are ready to advise customers and provide a solution for these new materials.”
In line with these ambitions, Domino’s laser team obtained samples of Futamura’s market-leading NatureFlex cellulose films to determine which of Domino’s laser coding solutions would provide the best option for manufacturers utilising these new substrates on their production lines.

Coding requirements of compostable films
NatureFlex films have been developed for use in food packaging applications, to meet the growing demand for environmentally responsible packaging. The films are designed to meet all the global standards for industrial composting, including BS EN13432, and are certified as home compostable under the OK Compost Home standard.
Typical NatureFlex applications include fresh produce, such as fruits and vegetables, where the film can also act as a wrapper for composting any left-over food waste or vegetable peelings. NatureFlex films are also widely used in ambient food and beverage applications – such as confectionery and tea and coffee – as the inner liner within a cardboard container.
Exact coding requirements for conventional plastic films vary depending on the specific application, with codes often only necessary where a film is used as part of a product’s outer packaging. However, with compostable products such as NatureFlex, direct printing may be required for both internal and external films, so brands can include messaging to help advise consumers of how best to dispose of the packaging.
“Brand owners are always looking at ways to communicate with their consumers on their packaging” says Amaia Cowan, Business Development Manager – EMEA, Futamura UK. “All of our NatureFlex films are certified to prove their suitability for industrial and home composting. Many of our customers want to show the final packaging’s certification and additional disposal information on the film to help inform end consumers.”
The option of laser coding a simple message onto the NatureFlex flexible film is an attractive prospect as the coding method does not require adding any additional materials onto the compostable substrate so seeking certification of the final packaging should be straightforward.
How did Domino select the appropriate solution?
Domino’s coding experts analysed six different versions of NatureFlex compostable film to determine which laser coding solution would be the most appropriate option for further suitability testing.
“In the first instance, we carried out spectroscopic analysis for the substrates to determine which wavelength of light has the best interaction with the substrate material; this allowed us to determine which laser we should use for further testing,” says Stadler.
“Spectroscopy is an analytical technique that tells you the substrate materials’ response towards the laser – and through doing this, we identified the D-Series CO2 Laser coders as a possible solution for NatureFlex compostable films.”
The next step was to code the samples – this was carried out using one of Domino’s D120i CO2 laser coders.
“I was expecting to see a result similar to the effect that we get when laser coding PET bottles – which is an etched, engraved code on the very top of the substrate,” says Stadler. “In fact, the effect of the laser was to change the colour of the film, resulting in a crisp, white code.”

The films were then subjected to further suitability testing to ascertain the minimum laser strength and code speed required to achieve a readable code. The results were encouraging, revealing that Domino’s lowest-power CO2 laser, the D120i, was capable of coding the substrate with just 40% laser power, even when operating at high production speeds.
“Typical flexible film applications, such as those used by NatureFlex customers, will rarely necessitate maximum coding speeds. However, based on our analysis, we can see that NatureFlex films can be coded effectively with the D120i when operating at very high production speeds, where required,” says Stadler.
How did Domino ensure that the laser did not compromise the film’s integrity?
Following coding with the D120i, the NatureFlex films were analysed using 3D microscopic imagery to provide a closer look at how the code was formed.

“With this type of 3D image, we can measure the depth of the laser engraving to ensure that the substrate is not perforated or compromised. The laser had a foaming effect on the NatureFlex films, that led to an increase in the film thickness in the irradiated areas by approximately 11.5 micrometres.”

The microscopic imagery determined that no structural damage was inflicted upon the film – even in places where the vectors of individual letters or numbers met (for example, in the overlapping curves of the B in the image above), which would have been subjected to the highest amount of laser power.
In addition to the 3D microscopic imagery, the samples were also analysed using FT-IR spectroscopy to determine whether the laser coding resulted in any chemical additions to the material. Samples of uncoded and coded NatureFlex film were subjected to different infrared wavelengths, and the results of the two samples were compared.
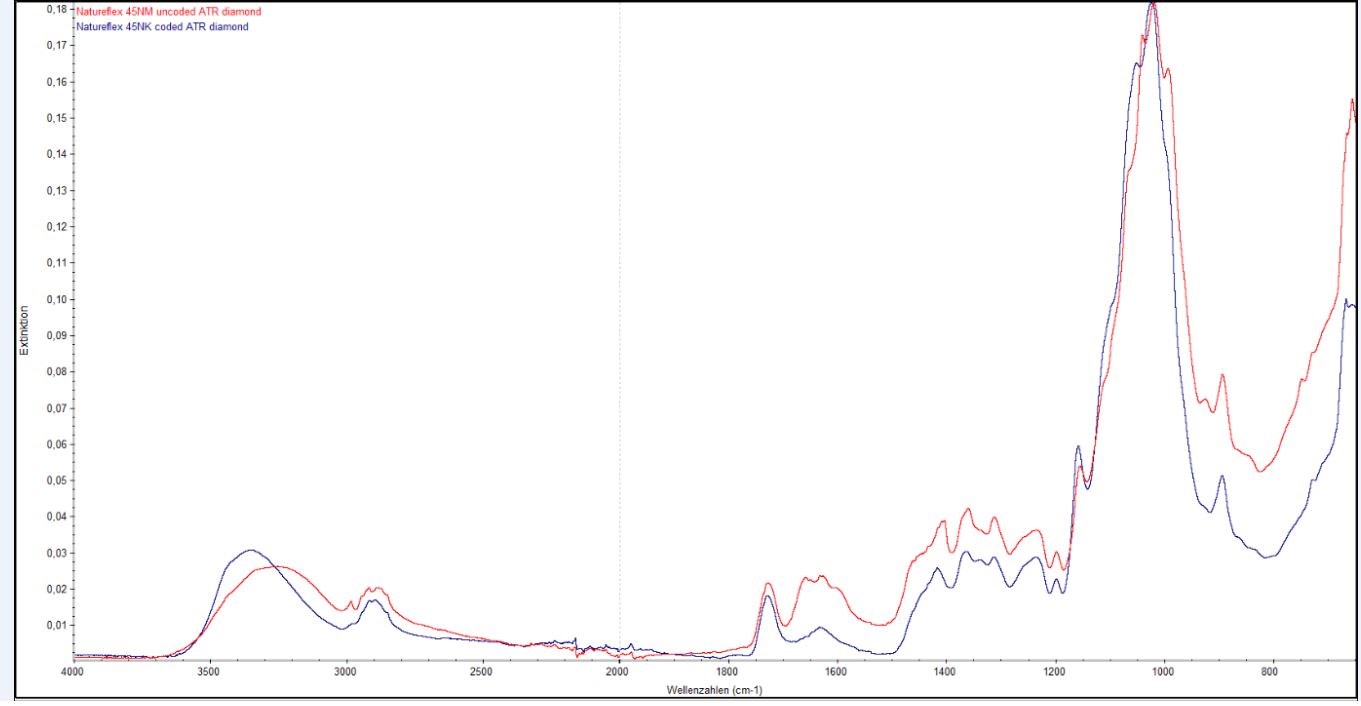
The chart above shows the results of the infrared imaging.
“Here, we have two curves, the curve in red is the uncoded material, and the curve in blue is the coded material. You can see the number of peaks and the overall shape of these curves is the same, which indicates that the laser coding process did not generate any additional chemistry within the material,” says Stadler. “From these tests, we can certify that the code on the material is the result of a physical change in the material and not a chemical change. The material itself is the same.”
The coded materials were returned to Futamura for further evaluation and preliminary assessment of the coded films’ moisture barriers. The data suggested that the coding had little effect on this specific property.
The Domino difference
“Product coding and marking is important for our customers – however, this is outside of our area of knowledge, and so we were very pleased to work with a company like Domino on this project,” says Cowan.
“We were reassured by Domino’s scientific approach to substrate testing and coding and willingness to provide us with the results and assurance that we needed to confirm that Domino’s CO2 laser coders are a suitable solution for our compostable films.”
The quality and clarity of the codes make laser coding on NatureFlex flexible film a good choice for food manufacturers looking to create both simple codes, such as best before dates and batch codes, as well as more complex designs and messaging, including graphics and scannable 2D codes.
“The results from the project are very positive,” says Cowan. “This new method of coding will enable the inclusion of a message to consumers on the film itself, without printing. As no additional materials are added to the compostable films, seeking certification of the final packaging will be straightforward.”

Looking to the future with Domino lasers
The project with Futamura and NatureFlex compostable film is an exciting development in laser coding for sustainable substrates – and is just one example of how Domino is working to support customers on their sustainability journey.
“We want to remain at the forefront of developments in new and emerging packaging materials to ensure that we can continue to meet the needs of our customers in all industries,” says Stadler.
“We have a vision for our Laser Academy, as a substrate centre of excellence where we can invest in scientific testing and coding of new materials, based on our exploratory research, as well as direct customer requests.
“By taking a scientific, rather than a trial-and-error approach to laser coding, we can not only significantly accelerate the process of consistently and reliably creating an attractive, high-contrast code, but also ensure product safety and barrier properties are maintained – which is of great benefit to our customers.”
Domino is here to support the needs of any business looking to explore sustainable substrates and can test sample materials to provide recommendations for specific code requirements. Domino welcomes visits to the Laser Academy and other advanced testing facilities to demonstrate Domino technologies and their capabilities.
If you are currently looking into new sustainable substrates for your product packaging and would like to discuss Domino’s options for laser coding or any other coding and marking requirements, please get in touch.