Wells & Young’s Small Pack Continuous Improvements Leader Justin Adams explains: “Our previous coding and marking printers were early model machines, which we hadn’t upgraded. Due to the age of the machines we had a lot of maintenance problems, downtime was high and we had to have a back up machine for each printer in case any of them developed a fault.”
These difficulties, along with the added expense of service agreements and parts, meant that the cost of operating and maintaining its existing coding and marking equipment rose by 20% in 2011.
After getting the green light to replace the outdated equipment, Justin set about obtaining quotes from different coding and marking solution providers and comparing the different packages.
He says: “I had worked with Domino in previous roles so it was the first supplier I called to quote for the job as I had always been impressed with the quality and reliability of both its technology and the excellent customer care.
“When the proposals came back from the different suppliers the Domino team stood out for having really listened to my criteria and for having tailored their recommended solution accordingly.”
“Our investment in Domino solutions has saved us significant costs in terms of
maintenance, service agreements and machine downtime.”Justin Adams - Small Pack Continuous Improvements Leader
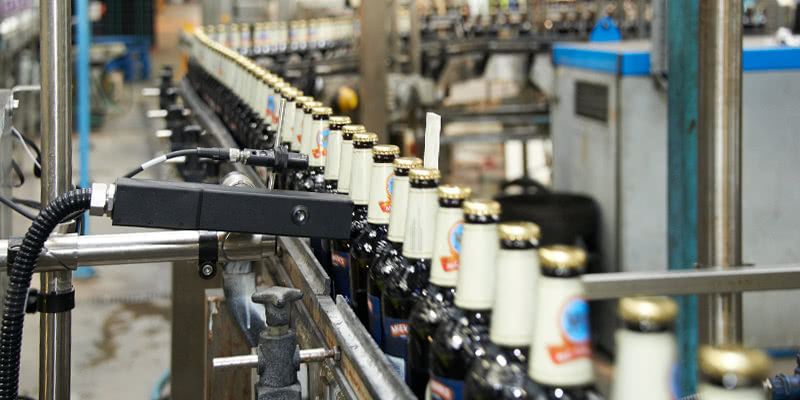
Justin was instantly impressed with Domino UK’s approach to his requirements and closer examination of the solutions offered by each potential supplier revealed a key difference which helped to swing the decision firmly in Domino’s favour.
Paul Johnson, Domino UK Area Sales Manager, explains: “Domino’s A-Series i-Tech printers are available with our SafeGuard five-year warranty. This warranty offers production convenience and uptime as the full cost of ownership for parts and labour are covered for the five year period. The only additional cost for running the printers is the inks.”
“Our calculations revealed that, by choosing Domino, our annual running costs, including ink, would be 50% less than if we opted for one of the other suppliers,” adds Justin.
The new A-Series ink jet printers, which have been fully operational since last summer, are being used for both the factory’s bottling and canning lines.
On its bottling lines the brewery uses the A300+ Opaque printer with Domino’s 253WT white ink to apply twin lines of code onto glass bottles (brown and clear), which range in size from 330ml to 670ml.
The bottles are then placed into a case, via a Kister packaging line, which is then also coded with an A420i printer, using Domino 2BK009 black ink.
On the canning line, the Domino A420i printers are used, with a six metre conduit, to print twin lines of code onto the cans. An OCME tray filler then places the cans onto a tray, with both sides of the tray coded using two of the company’s new A420i machines while another of the company’s new A-Series ink jet printers is to be used as a spare, in case of any additional requirements.
Justin explains: “Our investment in Domino solutions has saved us significant costs in terms of maintenance, service agreements and machine downtime.
“We’ve been pleased with the sales and service we’ve received from Domino on this project and are now considering further investment in some of their other print and apply label solutions.”